
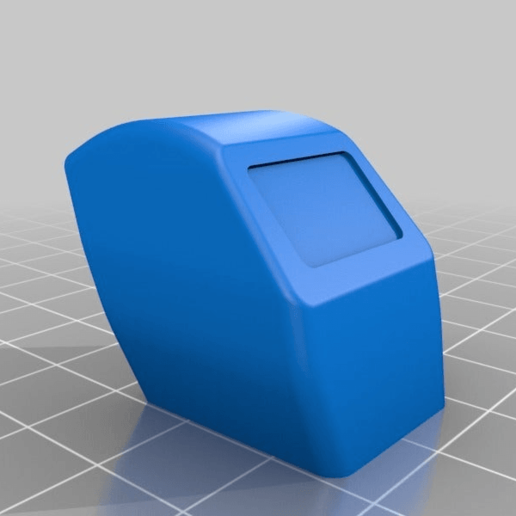
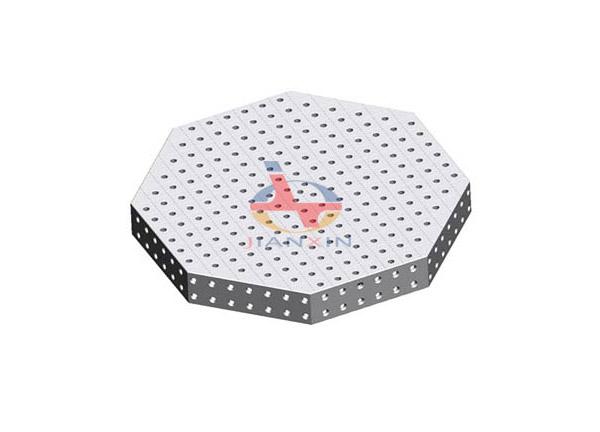
Multi Jet Fusion parts are made of thermoplastic materials and can be re-melted and re-formed once printed. We offer this for free to our customers and can work with you to make sure you original design intent is maintained. At F3DP we utilize a specialized software called Magics that allows us to very easily and quickly split parts to make glue joints as needed. 008″ between parts for the glue, in addition to the minimum spacing between parts printed as assemblies (see above). Remember to leave an additional space of. If you plan to glue parts together, you are recommended to include interlocking features such as those shown in the pictures below: as a guide to position the parts, to help them to bond together, and to facilitate the gluing process. They can then be joined together by gluing, welding, or by pin inserts. Parts larger than the maximum build size can be printed with Multi Jet Fusion by splitting them into different parts. Solid part Hollow part Hollow part with drain holes At F3DP we utilize a specialized software called Magics that allows us to very easily and quickly hollow and add drain holes to parts as needed. We can also leave powder trapped in the parts, this helps save cost on complicated depowdering / plugging of parts but if the part needs to be dyed black this is not recommended as it causes the parts to float. 25″ and a minimum of 2 of them is recommended to allow for compressed air depowdering. The minimum recommended diameter of these drain holes is. If the parts printed are hollow, drain holes can to be added to the design to remove the unsintered material. One down side to consider is that due to the parts being hollow they can be a bit weaker. Parts can be printed hollow, this greatly recuses the amount of heat that builds up in the part during the printing process allowing for more accurate parts and also allows them to be lower cost (less raw material and fusing agent are used).
